„Connecting Technologies“ bedeutet Module eines Studiengangs zu verknüpfen, Studierende und Lehrende miteinander zu vernetzen, sowie Anwendende mit den Prozessen interagieren zu lassen.
Angewandte Forschung
GoetheLab
Das GoetheLab for Additive Manufacturing hat das Ziel die Möglichkeiten und Potenziale der additiven Fertigungstechnologie durch anwendungsnahe Forschung und Wissenstransfer auszuschöpfen und weiter zu entwickeln.
Dabei richtet sich die angewandte Forschung im GoetheLab an der Weiterentwicklung additiver Fertigungsprozesse entlang der physischen und digitalen Prozesskette aus. Gemeinsam mit Partnern aus Forschung und Industrie werden schwerpunktmäßig die Materialklassen Kunststoff und Metall betrachtet.
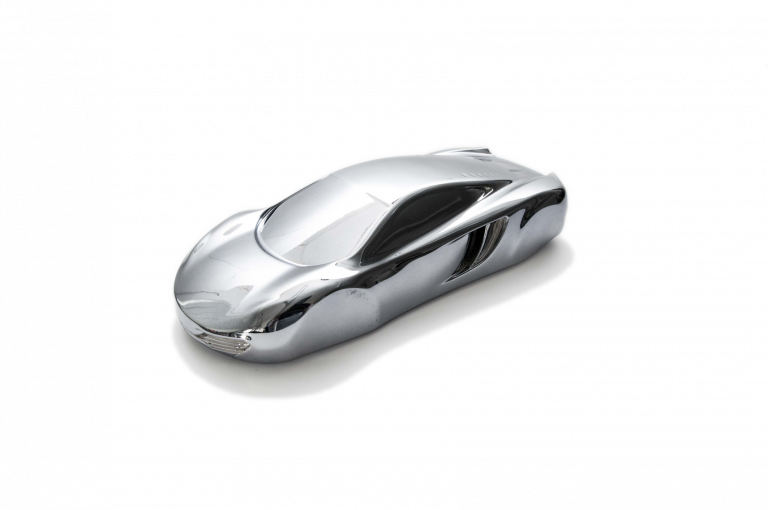
Forschungsschwerpunkte
Das GoetheLab for Additive Manufacturing legt einen Schwerpunkt auf folgende Forschungsaktivitäten und Materialklassen. Gerne können Sie sich als Unternehmen über individuelle Möglichkeiten in Form einer Kooperation informieren. Falls sie Student:in sind könnte für Sie die Möglichkeit einer studentischen Abschlussarbeit interessant sein.
- Grundlagenforschung
- Material- und Maschinenentwicklung
- Machbarkeitsstudien
- Integration des Fertigungsverfahren in industrietypische Umgebungen
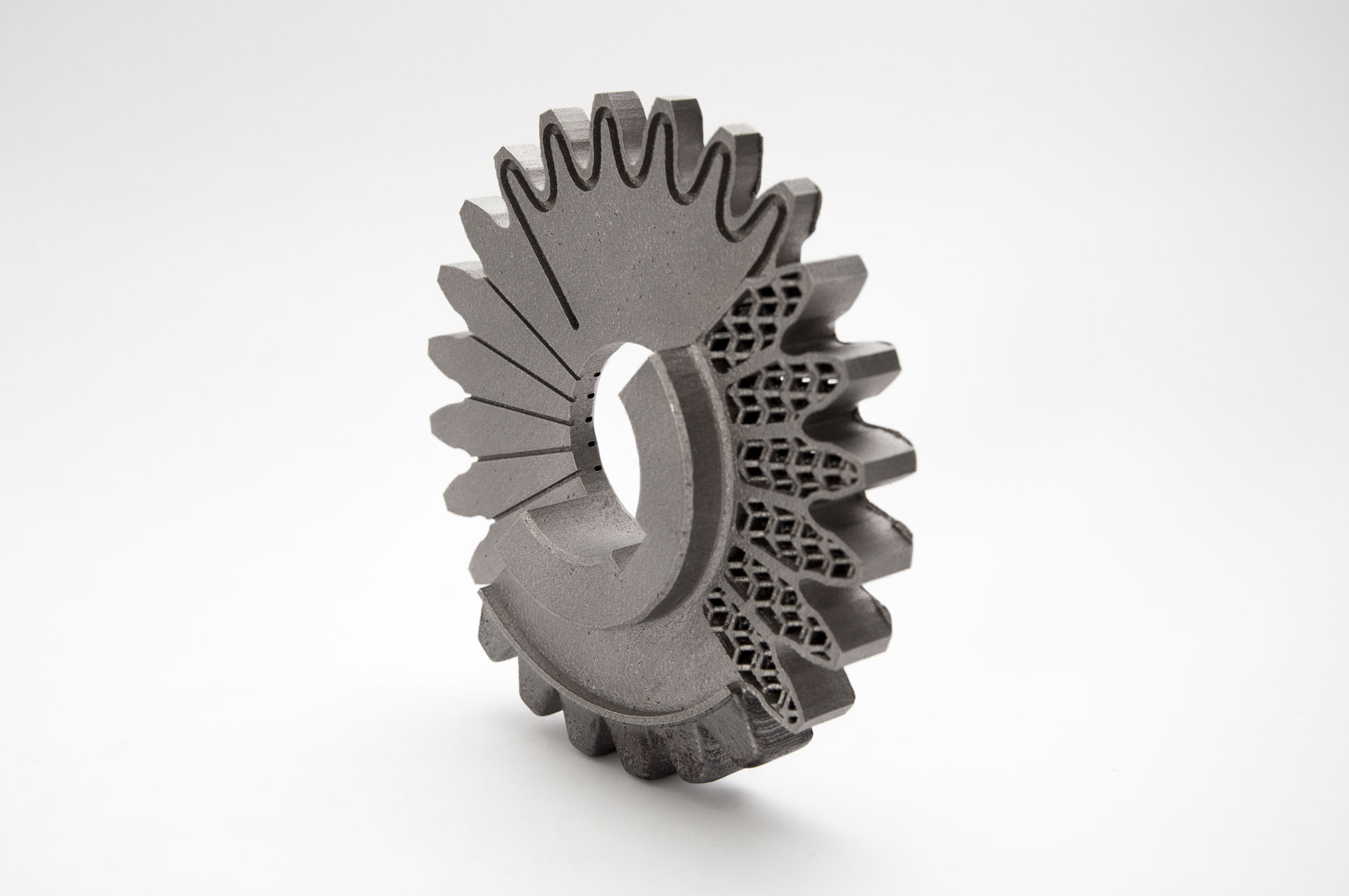
Metall
- Großvolumige LPBF-Bauteile
- Leichtbau großvolumiger LPBF-Bauteile
- LPBF-Bauteile mit integrierter (passiver) Kühlung
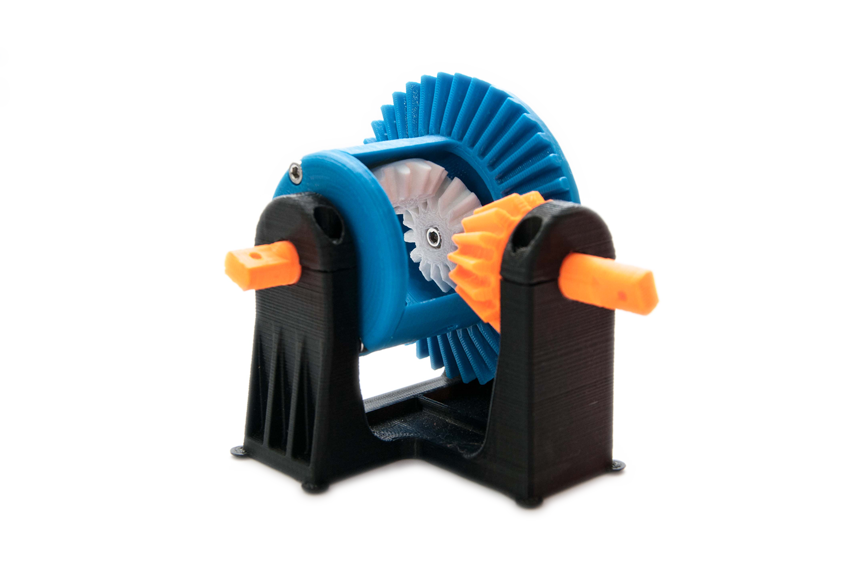
Kunststoff
- High Performance Polymers (Bspw. PEEK)
- Druck von faserverstärkten Kunststoffbauteilen
- Leichtbau struktureller AM-Bauteile aus Kunststoff
Forschungsprojekte
Im Forschungsvorhaben AlPhaMat werden auf Basis des TwoCure Verfahrens gemeinsam Herausforderungen und Limitierungen bei bekannten Werkstoffen beseitigt und neue Formulierungen von Photoharzen untersucht.
Im Forschungsvorhaben „Infused Thermal Solutions“ (ITS) wird in Zusammenarbeit mit Prof. Dr. Markus Czupalla vom Fachbereich Luft- und Raumfahrttechnik die Verwendung von bereits erprobten Latentwärmespeichern in Kombination mit der additiven Fertigung untersucht.
Im Rahmen dieses Projekts (FB8 und FB6) werden die verschiedenen Möglichkeiten der Funktionsintegration (Aktuatoren, Sensoren, Batteriezellen, Crashelemente, etc.) näher untersucht und deren Potenzial zur schnellen Erreichung einer Serienreife bestimmt. Der Fokus liegt auf dem additiven Extrusionsverfahren, dem sogenannten Fused Layer Modelling, sowie dem Einsatz von Kurz- und Endlosfasern.
In Gesellschaft und Industrie ist ein zunehmendes ökologisches Bewusstsein vorhanden, was in einem Umdenken hinsichtlich einer ökologischen Umweltwirtschaft resultiert. Diese Veränderungen im Konsumverhalten …
Ziel dieses Projektes ist es, die LASER.region.AACHEN zukünftig mit gut ausgebildetem Personal zu versorgen.
Große Bauteile für das Wasserstoff-FCE von Ecogenium Ecogenium ist ein Team motivierter Studenten, der FH und RWTH. Im Bereich der Wasserstoffmobilität nimmt …
Im Rahmen der Lehre bietet das GoetheLab den Studenten praxisnahe Einblicke und Möglichkeit, im Rahmen ihres Studiums an einem faszinierenden Projekt teilzunehmen. …
RTe Journal
Das RTe Journal, Rapid Technologie electronic Journal, wurde neu aufgesetzt und ist mit einem neuen wissenschaftlichen Beirat wieder auf der Suche nach interessanten Veröffentlichungen. Sie suchen eine von Expert:innen begutachtete Veröffentlichung oder wollen selber eine Veröffentlichung einreichen?
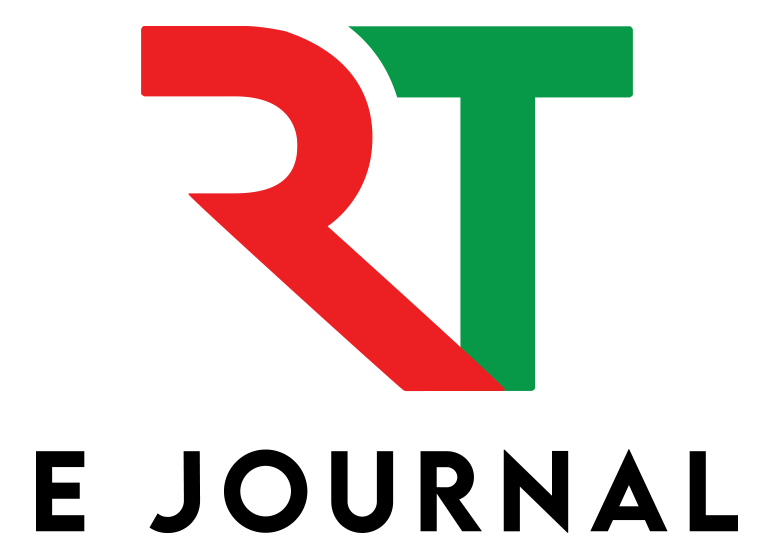
Promotionen
Basic research on direct injection molds made from high performance plastics
Kooperierende Hoschule: TUC-Technical University of Cluj-Napoca (Rumänien)
Die fertigende Industrie ist zunehmend auf innovative Technologien angewiesen, um schnell und flexibel Güter zu produzieren. Hier kristallisiert sich die Additive Fertigung als einer der jüngsten und wichtigsten Fertigungsverfahren heraus. Das sogenannte Schichtbauverfahren, auch unter dem Begriff 3D-Druck bekannt, ermöglicht durch die Verfahrensart und diversen Materialien ungeahnte Möglichkeiten der Fertigung. Nahezu jede Geometrie ist mit nur einer Anlage realisierbar. Mit dieser Technologie können Prozessketten entscheidend beeinflusst und verkürzt werden. Dies reduziert die Fertigungszeit, kann den Einsatz von Ressourcen minimieren, reduziert den maschinellen Aufwand und folglich auch die Kosten.
Diese Eigenschaften sind für den Einsatz bei der Werkzeugherstellung überaus vorteilhaft. Die Herstellung eines Spritzgusswerkzeugs ist sehr kosten- sowie zeitintensiv. Bei der Auslegung eines Werkzeuges wird ein fundiertes Knowhow vom Konstrukteur und vom Anlagentechniker benötigt. Doch auch mit viel Erfahrung sind mehrere iterative Schritte notwendig, um zum endgültigen Werkzeug zu gelangen. Die Entwicklungsdauer ist demnach enorm.
An dieser Stelle soll die additive Fertigung ihren Einsatz finden und die Möglichkeit zu einer Effizienten Werkzeugentwicklung eröffnen. Ferner soll hierzu der Einsatz von sogenannten Hochleistungspolymeren verhelfen. Die hohe Temperaturbeständigkeit und die hohen mechanischen Eigenschaften sind dabei das wichtigste Auswahlkriterium für den geplanten Einsatz als Werkzeugmaterial.
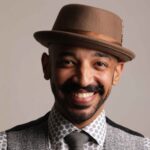
Karim Abbas
Promotionsvorhaben
Research on producing complex metal parts by Laser Powder Bed Fusion, to be welded onto larger components
Kooperierende Hoschule: TUC-Technical University of Cluj-Napoca (Rumänien)
Das additive Fertigungsverfahren Laser Powder Bed Fusion bietet ein herausragendes Potenzial zur Herstellung konturnaher funktionsintegrierter Bauteile aus metallischen Werkstoffen. Durch den schichtweisen Aufbau begegnet das Verfahren den Forderungen nach steigender Komplexität und steigender Flexibilisierung herzustellender Produkte. Trotz der Vorteile dieser jungen Fertigungstechnologie wird sie aktuell vornehmlich zur Herstellung von hochwertigen bzw. kostenintensiven Bauteilen in kleinen Losgrößen eingesetzt.
Industrielle Anwendungsbeispiele finden sich primär in den Branchen Luft- und Raumfahrt, Energietechnik und Medizintechnik. Ursache für den derzeitigen limitierten industriellen Einsatzgrad der LPBF-Technologie sind die fehlende Einbindung des Verfahrens in die vorhandenen industriellen Prozessketten, die geringe Produktivität und die eingeschränkte herstellbare Bauteilgröße.
Der in dieser Promotion verfolgte, vielversprechende Ansatz diesen Herausforderungen zu begegnen, beinhaltet die intelligente Kombination des LPBF-Verfahrens mit dem Fügeprozess Schweißen. Ziel der Arbeit ist die Entwicklung einer ganzheitlichen Prozesskette zu Herstellung von großvolumigen und funktionsintegrierten Bauteilen mittels additiver Fertigung und Schweißen.
So könnten Bauteilbereiche, die komplexe und funktionsintegrierte Elemente enthalten, mittels LPBF gefertigt werden, während andere Bereiche, die konventionell (Zerspanung, Umformen) kosteneffizienter gefertigt werden können, mit bestehenden Fertigungsverfahren hergestellt werden. Außerdem ist es denkbar, den möglichen Bauraum von LPBF-Konstruktionen durch das Verschweißen von mehreren LPBF-Teilen zu vergrößern.
Dem gegenüber stehen viele metallurgische sowie prozesstechnische Hindernisse, die im gegenwärtigen Stand von Wissenschaft und Technik noch nicht ausführlich diskutiert wurden. Die ersten Schritte des Vorhabens beinhalten, nach einer tiefgehenden Recherche, die Anpassung des LBPF-Prozesses zur Reduktion resultierender Eigenspannungen. Materialsimulationen werden ebenso Einsatz finden, wie eine detaillierte Betrachtung der auftretenden Temperaturgradienten entlang beider Fertigungsprozesse. Gestützt durch regelmäßige metallurgische Untersuchungen wird versucht Verzug zu minimieren und metallurgisch vollständige Verbindungen zu erzielen.
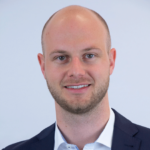
Fabian Eichler